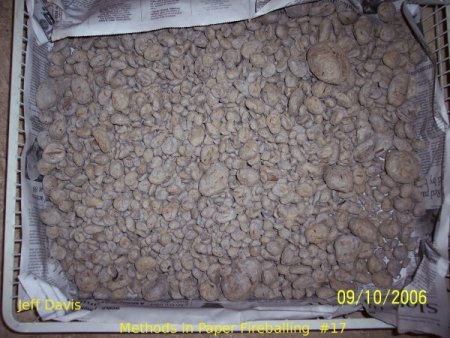
mpf17: Picture 17
Note: click on picture for full size.
This article explains the various methods that I have used to make paper fireballs. The most practical method is what I call the "rock & roll" method. The end product can be seen in the above picture 17.
Basically the old methods involved the below steps:
Old Method | |
# | Step |
1 | Soak paper in water. |
2 | Process with disposal (re-pulp). |
3 | De-water. |
4 | Ball in cement mixer. |
5 | Dry. |
In picture 1 you can see the paper being soaked in water. More time is better than less time, two weeks seems to work OK for me. Here I am using a plastic 55 gallon drum. I have found that this drum has poor ergonomics, it's too deep for one to remove the last third of the paper. My solution, as can be seen in this picture, was to cut off the top third of the barrel and use that section underneath the remaining portion, in order to raise the barrel to a proper working height.
The next step was to re-pulp the paper with the aid of a garbage disposal as can be seen in pictures #2 and #3. The watery slurry from the disposal is shown in picture 4. {This has been obsoleted by the "rock & roll" method}
Here we are dew atering the slurry (picture 5). This is a plastic 55-gallon drum with the top cut open and a screen mesh fasten over this opening. The slurry is poured on the screen and the water is collected in the drum.{This has been obsoleted by the "rock & roll" method}
You can see the wet paper fibers after the dew atering, in picture 6. The fibers are still very wet. From this point there was three methods to produce paper fireballs in the rotating drum/agglomerator. (1) If the moisture was just right the pulp/fibers would break up into fireballs/agglomerations. This was very hard to do correctly. (2) The next method was to add something dry like sawdust to the fiber/pulp, as it was being balled in the agglomerator. I think of this as the opposite of dust agglomerating. When one balls charcoal dust you add the liquid binder to the dusts as it is balling. (3) The last method was the most reliable of the three and that was to simply crumble the pulp into the agglomerator and the agglomerator served simply as a sharper, more or less. {This has been obsoleted by the "rock & roll" method}
"Rock & Roll" Method | |
# | Step |
1 | Soak paper in water. |
2 | Place wet paper w/rocks in cement mixer and mill. |
3 | Remove rocks after agglomerations have formed and ball somemore for final shape. |
4 | Dry. |
I should also reinforce that this is newspaper feedstock, not any other kind of paper. Other kinds of paper may work if retted first or soaked for a much longer time period or if a larger ball/rock mill is used.
One can see the specifications of the cement mixer/agglomerator that I used, in picture 7. In picture 8 you will see the Kill-A-Watt meter that was used to measure the electric used for these experiments. This device will display volts, amps, watts, volt/amps, Hz, power factor, kWh and hours. The cost is about $35.00 US. Picture 9 shows the rocks used for the ball milling.
Picture 10 shows two kitty litter pails full of water soaked newspaper. I processed one bucket at a time. A five-gallon bucket is not much larger then a kitty litter bucket and the cement mixer has no problem processing a five-gallon bucket load if not more. It seems that a larger load takes about the same amount of time to process as a smaller load but if loaded with two buckets of paper the mixer becomes over loaded and the time to process the paper greatly increases. Also if one over loads the mixer the paper fireballs do not shape well and you may need to re-roll them. In other words, there seems to be an optimum load for the machine..
This is the start of the ball milling. Starting to break up the paper (pictures 11, 12, 13 & 15).
Agglomerations are starting to appear in picture 13. The moisture content (MC) of the feedstock has a bearing on how much time this process takes and the shape, size and surface texture of the fireball. Let's examine two examples:
The paperfeed stock has been soaking for at least two weeks and is easily falling apart: I first remove the soaked paper from the modified 55-gallon drum and place it in the bucket. Next I have found that it works best to drain the excess water from the bucket. Now the soaked paper is ready to be rock/ball milled.
The paper feedstock has been soaked for about three days. It is completely wet but not falling apart. Just like above, I remove the soaked paper from the modified 55-gallon drum and place in it in the bucket but this time I do not drain the excess water from the bucket. Now the soaked paper and water is ready to be rock/ball milled.
In other words, if the paper has not been soaked for very long a little extra water in the rock/ball mill is of advantage.
Below in table 1 you will find the Kill-A-Watt meter data. In regards to V, A, W, VA, pf and Hz they are all just a snap-shot reading not an average. So I could have recorded the amps at 5.02A and when I recorded the Watts the Amps could now be 4.85A. But, the kWh is a total reading.
Table 1 | Total | Total | ||||||
State of Agglomerator | V | A | W | VA | pf | Hz | kWh | minutes |
no load (mixer is empty) | 119.3 | 5.7 | 202 | 676 | 0.29 | ? | n/a | |
with only rocks (no paper) | 118.5 | 5.65 | 246 | 667 | 0.36 | ? | n/a | |
kitty litter bucket #1 milling (w/rocks) | 120.4 | 5.76 | 288 | 694 | 0.41 | 59.9 | n/a | |
kitty litter bucket #1 balling (no rocks) | 120.4 | 5.73 | 270 | 692 | 0.38 | 59.9 | 0.08 | 18 |
kitty litter bucket # 2 milling & balling | ? | ? | ? | ? | ? | ? | 0.09 | 20 |
five-gallon bucket milling (w/rocks) | 117.3 | 5.52 | 250 | 647 | 0.36 | 59.9 | n/a | |
five-gallon bucket balling (no rocks) | 115.3 | 5.33 | 251 | 616 | 0.40 | 59.9 | 0.08 | 20 |
The rocks have been removed at this point as can be seen in picture 16.
In picture 18 you can see that the drum is rotating hence the start of the final shaping.
Close-up of the final shaping phase, see picture 19.
Just out of the mixer, in need of drying, in picture 20.
Picture 21 shows the angle of repose.
This is a picture (22) of a batch done a week before, almost dry, it is the amount from a five-gallon bucket.
Below in Table-2 you will find more data. In this article retentivity is the ability of a fireball to retain oil or WVO.
Table 2 | |
Angle of repose | ~ 20 |
Bulk density (medium sized) | 177g / Liter |
One 5-gallon bucket of wet paper | ~1.4kg of air dried fireballs |
Particle density | 0.248g / cm^3 |
Retentivity (oil) | OK |
In conclusion; I would like to express that I (a mere pip-squeak in the field of biomass) was able to see more clearly and further by standing on the shoulders of GIANTS like Tom Reed, John Tatom, Bhatacharya, Richard Stanley et al. The true inventor of the paper fireball is the List or more exact lists (stove, gasification and bioconversion). Below you can read about some of the history/inspiration behind the paper fireball.
Best wishes,
Jeff Davis
Helifuel:
(Elements II Briquetting and Agglomeration, Koerner & MacDougall p. 93)
To convert high sulfur coal into clean fuel, McDowell-Wellman developed Helifuel, a mixture of ground coal and limestone, pelletized in a disc, followed by carbonizing or pyrolizing in a grate type sinter machine to produce hard, smokeless pellets of low ash and sulfur content for combustion or gasification (written about in 1979).
I also suspect that coal fines were ball agglomerated before Helifuel.
Tom Reed wrote:
We do a lot of re-discovering the wheel in this world and should keep it to a minimum if possible.
In the mid 1980s John, working for USAID designed a Georgia Tech type "BIG BLUE" pyrolyser for developing countries. It made tar and char.
He developed a 55 gal (200 l) charcoal briquetter that made "fire balls",
about 3 cm in diameter. I have a few in my laboratory charcoal collection.
They do not break up when dropped from 2 m.
A slurry of starch (5%??) is added to half a drum of chardust lying
horizontally on rollers. Drum is closed and rotated with a handcrank.
The process is analogous to making bread, when the first stage of water
absorption produces LUMPS which eventually blend with the other
ingredients to form dough. I presume there is a modest amount of art
involved in knowing when to stop cranking.
I believe that Bhatacharya at AIT has reports on this process. Hope we
hear from him, too.
TOM REED
Tom Reed wrote (Nov. 29, 2005):
Dear Jeff and All:
I found that newspaper went very nicely through my wife's disposal -
along with many other potentials for fuel.
TOM REED
Jeff Davis wrote (Nov. 21, 2005):
Dear Crispin,
I would like to find a use for all my old newspapers. So what do I do to
the paper. Run it through a shredder, or puts some water and paper in my
mixer with my rocks? How fine does the paper have to be?
Richard Stanley wrote: (NOV.30, 2005)
Jeff,
As concerned binding up charcoal fines, I have never tried a cement mixed
used as a ball mill, but in as much as we are using fine ag residue
fibers for our bonding rather than glues /resins / waxes / starches,
etc., I wonder if the addition of dried but wetted grasses/straws would
not work. The ball mill would indeed mash them into the fine defibrated
paste you need and it would tend to mix them into the charcoal fines,
quite well too. Problem is that you would not really gain density here.
You would require about 50% paper (by wt) to adequately bind up the
crushed charcoal...But then again you would not need any added binder.
If you try it please let me know how it works. I know of about 75 of us
interested in its outcome, on an open source basis, with due reference
to you, if it works.
Richard Stanley